
9 min read
Cost Centers: How to Understand and Optimize Them
Cost centers serve as critical components in any organization, offering a lens through which to analyze and manage expenses effectively. Read about the logic of cost centers and ways to manage them with maximum efficiency.
For procurement professionals, systemizing and optimizing cost centers is not just a matter of financial management; it's a strategic task for driving efficiency, controlling costs, and enhancing overall performance. In this article, we delve into the intricacies of cost centers and explore strategies for improvement.
Keep reading about:
- What Are Cost Centers?
- What Are Cost Centers For?
- Types of Cost Centers
- Optimizing Cost Centers: Strategies for Success
- The Role Procurement Software Plays
What Are Cost Centers?
There are a few types of cost centers, and most commonly relate to production or service. Examples include human resources or IT departments, manufacturing plants, or project teams. We will look more closely at the different types of centers and what they encompass later on.
Cost centers can include discretionary and non-discretionary expenses. The former can be easily eliminated without affecting the company's ability to function properly. For example, if your company has a gym membership program for employees, this would be considered a discretionary cost. The latter type of costs are essential to the company’s operation and cannot be controlled or eliminated without adversely affecting the company's ability to function properly. For example, salaries for accounting staff would be considered a non-discretionary cost.
What Are Cost Centers For?
From departments and divisions to projects and processes, each cost center is a focal point for financial analysis and accountability. By delineating expenses into separate cost centers, businesses gain visibility into the financial performance of individual units or activities. This also facilitates accountability, enabling managers to track expenditures, assess resource utilization, and evaluate performance against predefined targets. Furthermore, cost center data provides valuable insights into where resources are allocated and whether they align with strategic priorities.
Cost center managers bear no responsibility for the company’s revenue or investment. However, every cost center indirectly contributes to the business revenue by ensuring that business operations run smoothly while the necessary expenses are kept in line with the budgets. Cost center data is more relevant for internal reporting in terms of evaluating operational and spending efficiency.
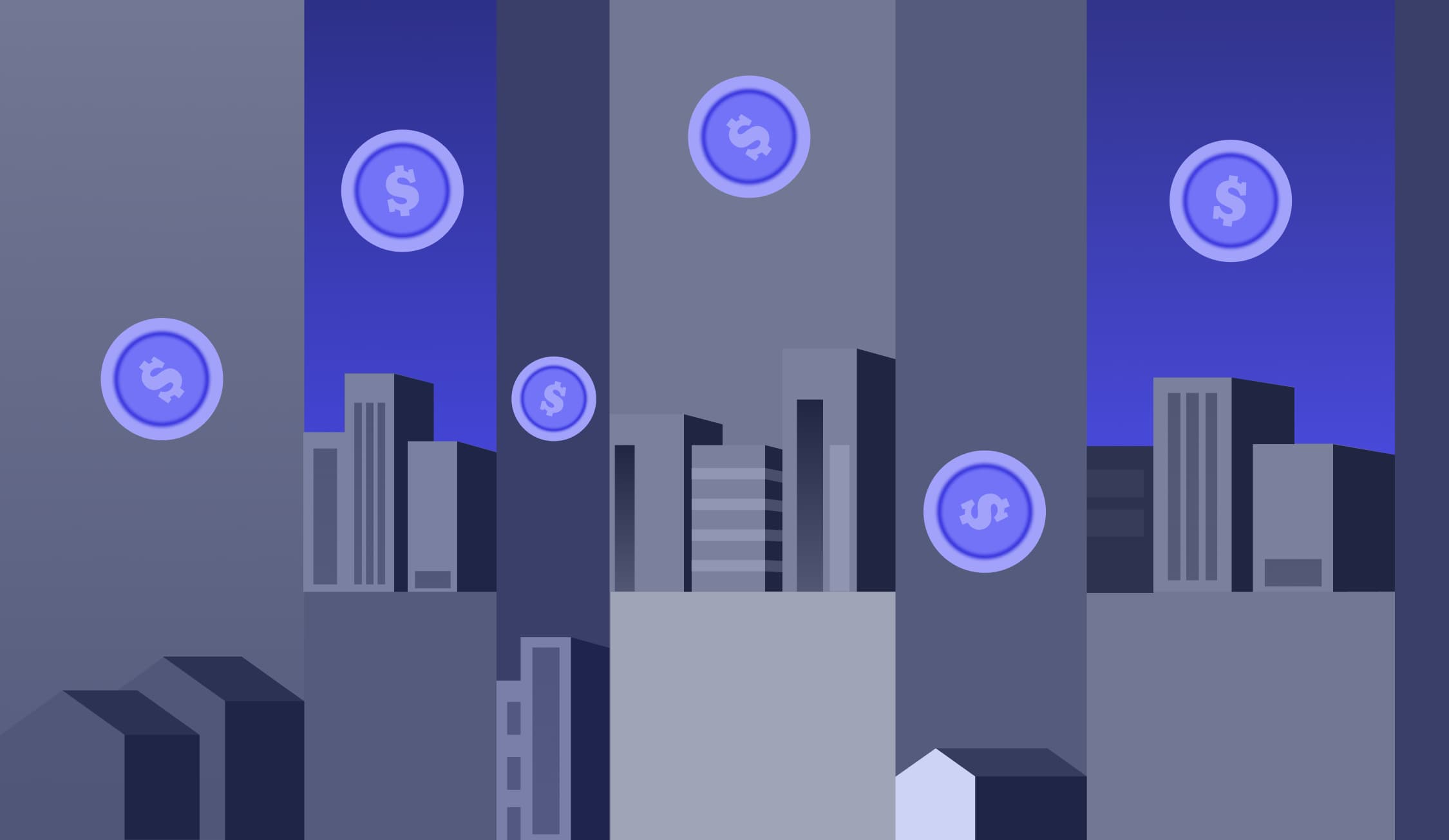
Types of Cost Centers
Companies craft their own cost centers according to production needs and operational specifics. Ultimately, cost centers should reflect the expenditures important for internal reporting. There are various angles from which to look at the expenses, which leads to shaping different cost centers. Let’s look at some of the typical ones.
Operational Cost Centers
Operational cost centers encompass costs related to people and equipment involved in a single activity with a clearly defined focus. Typically, such cost centers are organized as separate back-office departments within the company.
One example of such a cost center is the marketing department, which is responsible for promotional activities, advertising campaigns, and brand management. Its expenses may include advertising costs, creative services, market research, and promotional materials.
Another operational cost center present in virtually every kind of modern company is the IT department. This cost center is responsible for managing technology infrastructure, software systems, and support services. Expenses may include, for example, hardware purchases, software licenses, IT personnel salaries, and infrastructure maintenance.
Personal Cost Center
Personal cost centers include specific groups of employees. In contrast to the company department, as described earlier, a personal cost center wouldn't concern tangible resources. This type of cost center concerns solely the expenses related to personnel and doesn’t include expenditures on machinery, supplies, or other commodities.
Service Cost Center
A business might want to split its cost centers according to what service is being provided to the company. These can be security or janitorial services, for example. Another example of a service cost center might be the recruiting department.
Machinery Cost Center
Machinery cost centers include all of the non-employee expenses. These might be equipment costs and any expenses associated with them, such as: upfront purchasing, maintenance, and repair costs, and any other expenses related to the machinery involved in the production process. An example of a machinery cost center would be a manufacturing plant without employee expenses.
Locational Cost Center
Another way to look at the company cost centers is to consider expenses by location. A company might want to consider costs for the specific branch or region. For instance, a car manufacturer might need to consider the total cost of running their Chicago plant — and everything included in that would be the location cost center.
At the same time, the company might need to consider the machinery cost for a specific location. This would mean narrowing down the focus even more and combining criteria for location and machinery cost center.
R&D Cost Center
A research and development center focuses on expenditures required for innovation and product development. Such expenditures may encompass research activities, prototype development, laboratory equipment, and personnel costs. An example of an R&D cost center would be the technology and personnel needed for the development of a new type of electric bicycle (before production and market delivery).
Manufacturing Cost Center
A manufacturing cost center is a facility where expenses are incurred for producing goods. Labor, raw materials, equipment maintenance, utilities, and overhead costs are allocated to this cost center.
Product Cost Center
This type of cost center includes all expenses involved in developing, manufacturing, and bringing to the market one specific product or service. A product cost centre manager focuses on allocating and tracking expenses across the whole production process. These can include R&D costs, raw materials, maintenance of production line, labor, and marketing costs.

Optimizing Cost Centers: Strategies for Success
Cost centers require financial injections in order to run smoothly and fulfill their objectives, so it’s important for the businesses to ensure that the money is allocated and spent efficiently. It is a comprehensive task that requires considering not only the immediate effects of decreasing expenses but also evaluating the possible future impacts of the implemented changes on the production outcome, product quality, and revenue.
Companies can optimize their cost centers by planning expenses meticulously and monitoring them more closely, enhancing workflow efficiency, and focusing on continuous improvement. Let’s look at some strategies to consider for optimizing cost centers.
Budget Management and Variance Analysis
Companies should develop robust budgets for each cost center, aligning financial allocations with organizational goals and priorities. Finance teams can make more informed decisions and prepare more accurate budgets by identifying key cost drivers and linking expenses to specific activities.
For every budget in use, the finance team should then implement budget controls and monitoring mechanisms to track spending in real-time. Together with the cost center managers, they establish key performance indicators (KPIs) to assess the performance of each cost center against predefined metrics.
Cost center managers can formulate expected KPIs by benchmarking against industry standards and confirming internal quality standards. With these standards in mind, they should compare actual expenditures to budgeted amounts. By conducting such analysis regularly, the company can then identify trends, anomalies, and areas for improvement and cost-optimization.
Resource Optimization and Utilization Review
Cost center managers should also assess resource utilization to identify any inefficiencies. Data to look at depends on the cost center type. For instance, useful information to consider might be equipment usage rate, inventory turnover, or employee productivity. Management should also conduct cost-benefit analysis and evaluate the return on the investments.
With a comprehensive understanding of how resources are used within the given cost center, management can eliminate redundant activities or purchases within the cost center, and relocate resources to more value-added tasks.
Procurement and Vendor Management
Procurement activities constitute a great part of the total company expenses, so as a part of cost center optimization, it's important to keep track of procurement costs. Cost center managers should cooperate with procurement teams to evaluate purchasing practices and vendor relationships to ensure optimal value for money.
Some of the best practices to optimize expenses include negotiating favorable terms and pricing agreements with vendors, consolidating purchases where feasible, and leveraging technology solutions, such as procurement management software. This way, companies can streamline purchasing processes and enhance transparency for each cost center, ultimately leading to better overview and control of the spending.
Continuous Improvement Initiatives
Introducing a company philosophy of continuous improvement is a universal strategy for every business aspect, including cost center optimization. By conducting regular process reviews and implementing lean practices, cost centre managers can stay flexible in the face of changing market demands, customer preferences, supply chain stability, and internal regulations that stem from the business landscape.
To start with, cost center managers should empower employees and other stakeholders to contribute to cost-saving initiatives by providing their feedback. Employees who have first-hand experience with processes within cost centers can help identify opportunities for saving money and improving spend efficiency. Cost center managers can also encourage feedback from customers and company leadership.
Open and honest feedback is the basis for improvement initiatives. It also helps the cost center manager define the guidelines for the future operational and spending priorities, and introduce specific changes to the daily workflows.
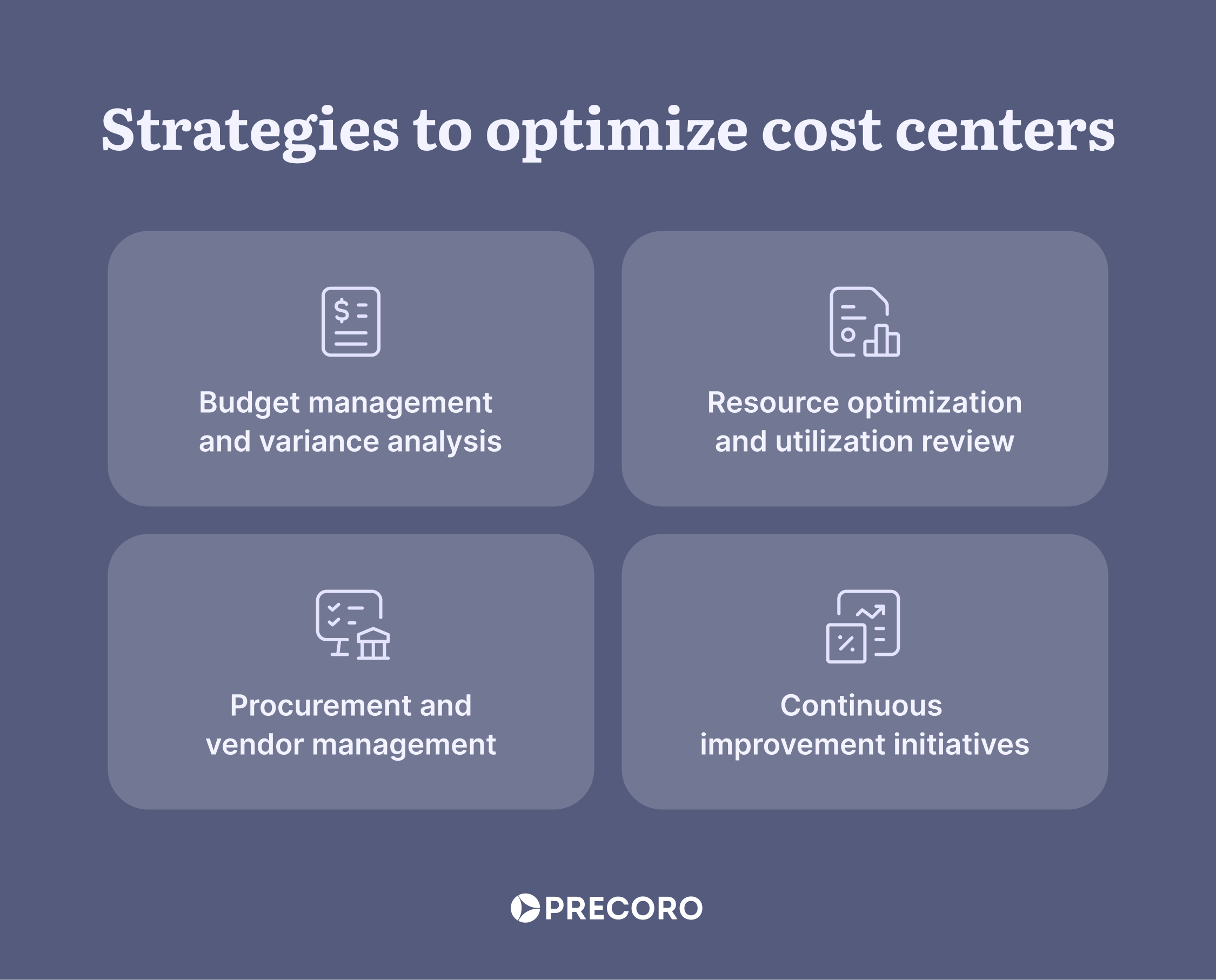
The Role Procurement Software Plays
Procurement software is undeniably important for optimizing cost centers by providing functionality to streamline procurement processes, enhance workflow visibility and accountability, and improve decision-making. With features such as spend analysis, budget tracking, vendor management, and performance reporting, procurement software empowers organizations to gain greater control over their expenditures and drive efficiency across cost centers.
By leveraging online procurement systems, businesses can automate routine tasks, reduce manual errors, enforce compliance with policies and procedures, and gain actionable insights into spending patterns and trends. This enables procurement professionals to make informed decisions, identify cost-saving opportunities, and optimize resource allocation within the cost centers to achieve better outcomes for the organization as a whole.
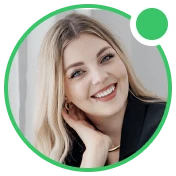
Understand, Optimize, Benefit
Understanding and optimizing cost centers is essential for organizations seeking to improve financial performance, enhance operational efficiency, and drive sustainable growth. It's relevant for companies across different industries, whether it's a construction business, renewable energy sector, hospitality, healthcare or other industries.
By implementing sound budget and resource management practices, fostering a culture of continuous improvement, and leveraging technology solutions like procurement software, businesses can effectively navigate the complexities of cost center management and finance allocation.
Frequently Asked Questions
A cost center is a department in a company where costs are incurred. Cost centers do not directly generate revenue, but they are necessary for a company’s uninterrupted functioning.
An IT department is an example of a cost center that is responsible for managing technology infrastructure, software systems, and support services. Expenses may include, for example, hardware purchases, software licenses, IT personnel salaries, and infrastructure maintenance.
Cost centers should reflect the expenditures important for internal company reporting. There are various angles from which to look at the expenses, which leads to different types of cost centers. Types of cost centers include operational, personal, service, machinery, locational, R&D, manufacturing, and product cost centers.
Ready to take control of your cost centers and maximize value across your organization? Contact us today to discover how Precoro can help you achieve your strategic objectives.